Opening the Power of Welding WPS: Approaches for Performance and Safety And Security in Manufacture
In the realm of construction, Welding Procedure Specifications (WPS) stand as the backbone of welding operations, determining the essential actions for accomplishing both effectiveness and safety and security in the manufacture procedure. Comprehending the ins and outs of WPS is vital to utilizing its full potential, yet several companies have a hard time to open the real power that exists within these records (welding WPS). By diving into the strategies that optimize welding WPS, a globe of improved efficiency and enhanced safety and security awaits those ready to explore the subtleties of this crucial aspect of fabrication

Value of Welding WPS
The value of Welding Procedure Specifications (WPS) in the manufacture market can not be overstated. WPS offer as an important roadmap that outlines the essential steps to make sure welds are carried out consistently and appropriately. By defining essential specifications such as welding processes, products, joint designs, preheat temperature levels, interpass temperatures, filler steels, and post-weld heat therapy requirements, WPS give a standard strategy to welding that boosts efficiency, high quality, and safety in construction processes.
Adherence to WPS assists in achieving harmony in weld quality, minimizing the likelihood of flaws or architectural failures. This standardization additionally helps with conformity with industry guidelines and codes, ensuring that produced frameworks satisfy the called for safety standards. In addition, WPS documentation allows welders to reproduce successful welding procedures, bring about consistent results throughout different tasks.
Fundamentally, the careful advancement and stringent adherence to Welding Procedure Specifications are critical for promoting the integrity of welded frameworks, safeguarding against prospective threats, and upholding the track record of manufacture firms for delivering premium items and solutions.
Secret Components of Welding WPS

Enhancing Performance With WPS
When maximizing welding operations, leveraging the key components outlined in Welding Procedure Specifications (WPS) becomes vital for optimizing and enhancing procedures performance. One method to boost performance with WPS is by meticulously picking the ideal welding criteria. By sticking to the details standards supplied in the WPS, welders can make sure that the welding devices is established correctly, resulting in premium and consistent welds. Additionally, following the pre-approved welding series described in the WPS can substantially minimize the time spent on each weld, inevitably boosting general efficiency.
Regularly evaluating and upgrading the WPS to incorporate any lessons discovered or technical advancements can likewise add to effectiveness improvements in welding operations. By embracing the guidelines established forth in the WPS and continually looking for means to maximize processes, fabricators can accomplish greater efficiency degrees and remarkable browse around these guys end outcomes.
Ensuring Safety in Fabrication
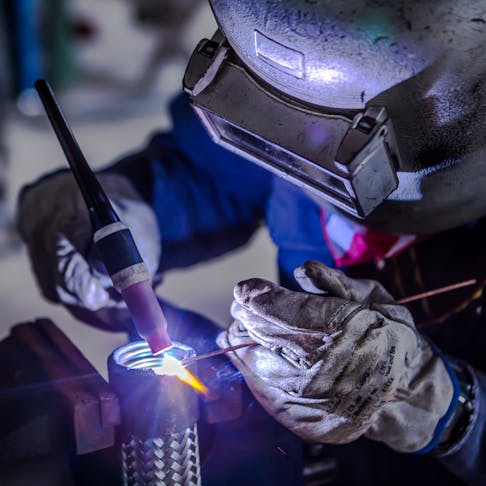
Guaranteeing safety in manufacture involves a diverse technique that includes different aspects of the welding process. Welders have to be geared up with suitable gear such as safety helmets, handwear covers, and protective garments to alleviate threats linked with welding tasks.
Moreover, adherence to correct air flow and fume extraction systems is important in keeping a healthy and balanced workplace. Welding fumes consist of hazardous substances that, if breathed in, can posture serious wellness dangers. Implementing effective ventilation procedures aids to lessen direct exposure to these dangerous fumes, advertising respiratory wellness amongst employees.
Regular equipment maintenance and inspections are also essential for making sure safety in fabrication. Faulty equipment can bring about crashes and injuries, highlighting the value of timely fixings and regular checks. By prioritizing security actions and cultivating a culture of recognition, fabrication facilities can produce a secure and productive workplace for their employees.
Carrying Out WPS Ideal Practices
To boost functional efficiency and make certain high quality outcomes in construction procedures, integrating Welding Treatment Spec (WPS) best practices is extremely important. Selecting the appropriate welding procedure, filler material, and preheat temperature specified in the WPS is critical for achieving the wanted weld high quality. Making sure that certified welders with the necessary certifications lug out the welding procedures according to the WPS guidelines is vital for consistency and reliability.
Verdict
In verdict, welding WPS plays a crucial role in guaranteeing effectiveness and security in construction procedures. By adhering to these approaches, organizations can open the complete possibility of welding WPS in their manufacture procedures.
In the world of manufacture, Welding Treatment Specs (WPS) stand as the foundation of welding operations, dictating the required steps for accomplishing both efficiency and safety in the construction process. By specifying crucial specifications such as welding processes, products, joint layouts, preheat temperatures, interpass temperature levels, filler metals, and post-weld heat therapy needs, WPS provide a standardized method to welding that improves performance, top quality, and safety and security in manufacture processes.
When optimizing welding operations, leveraging the vital elements detailed in Welding Treatment Specifications (WPS) ends up being essential for enhancing procedures and taking full advantage of productivity. (welding WPS)